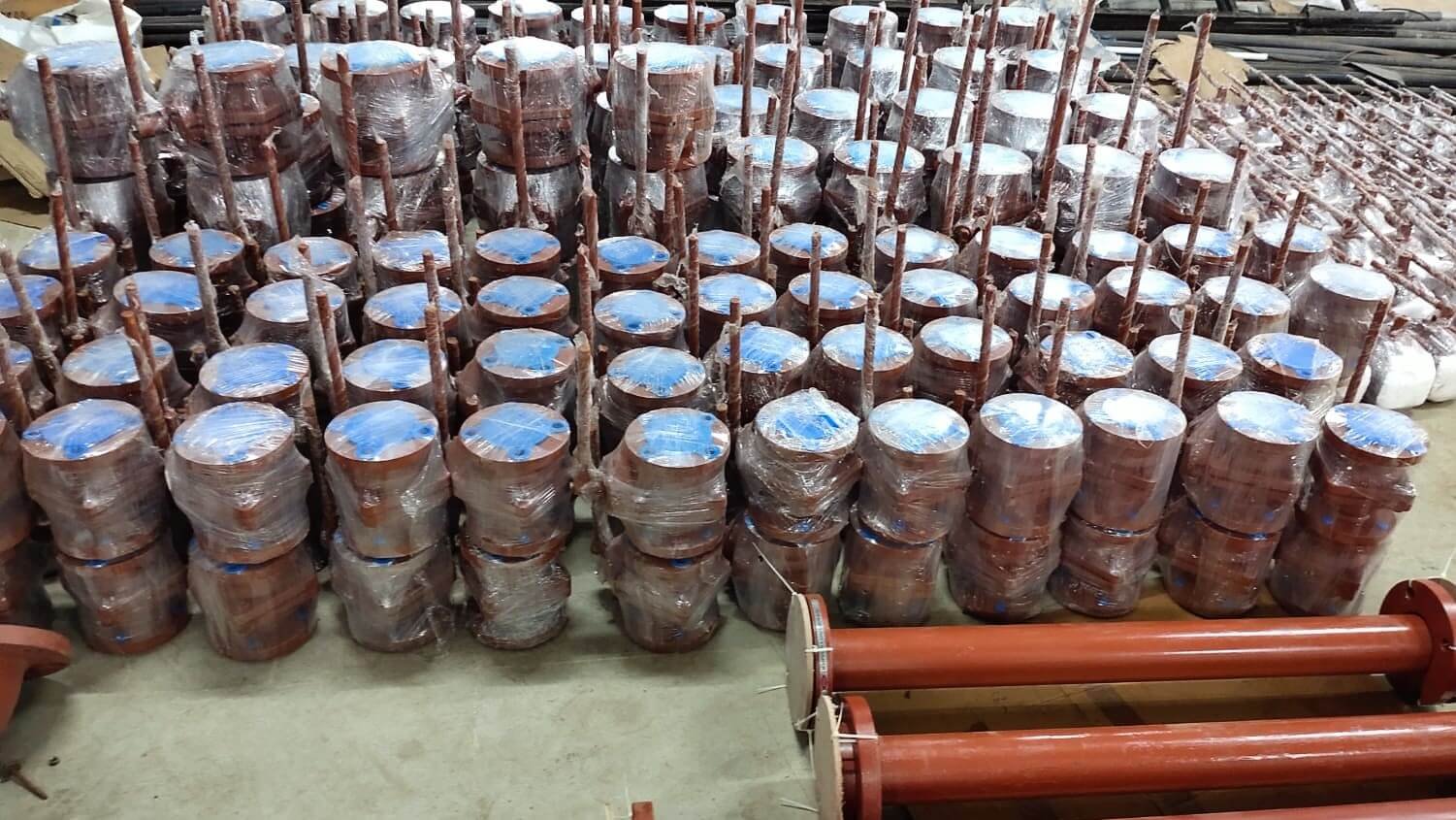
Polymer-lined Vessels, Tanks, HX & Components
A1-POLY Series
As the chemistry becomes more complex, the chemicals more corrosive and the purity tolerances tighter, Apical fluoropolymer-lined solutions often play a critical role in reliable processing.
Apical has taken years of validated field experience and added further insight from our deep network of industry professionals. We combine academic principles with cutting-edge design to provide equipment that can be relied on for years to come with safe, easy operation, high throughputs and consistent product.
Utilizing polymers like...
PTFE (Polytetrafluoroethylene)
FEP (Fluorinated Ethylene Propylene)
ETFE (Ethylene Tetrafluoroethylene)
PFA (PerfluoroAlkoxy)
PVDF(Polyvinylidene Fluoride)
...process systems can be built to handle highly corrosive chemicals while operating under deep vacuum, strong agitation and high temperatures (up to 150C). Naturally, these materials are common in chemical & pharmaceutical manufacturing. However, the need for extreme purities in semiconductor manufacturing has created significant demand for these fluoropolymers due to their chemical inertness and limited ion particle shedding.
Apical reactors have scale-up in mind, maintaining consistent ratios of dimension as they grow to ensure a reliable transition to larger processing. And, when scaling the ancillary systems, Apical works with trusted manufacturing partners known for their robust support staff and resilient equipment.
Considering these finer points is key to:
ultra-high purities
reliable throughputs
equipment lifespan
chemical mixture compatibility
successful process development
facility safety
efficient commercialization
Systems are built to DIN and cGMP standards for consistent production as well OSHA guidelines for safety. Apical takes industry guidelines seriously to ensure limited downtime, straight-forward audits and predictable operation.
The APICAL A1-POLY series has a wide range of vessel configurations with our unique design features and efficiency-minded details. Apical seeks to differentiate our systems through the thoroughness of our design and bidding process.
With that, Apical has the flexibility to fit systems to your scenario without compromise.
No myths about residence time, degradation or physics, no designs with built-in obsolescence, no exaggerations about system capabilities or pay-to-play obstacles to efficient processing.
Apical has tested a wide range of designs under production settings to pierce the veil and remove the mystique around chemical processing so business operators can focus on the customer and not a daily headache.

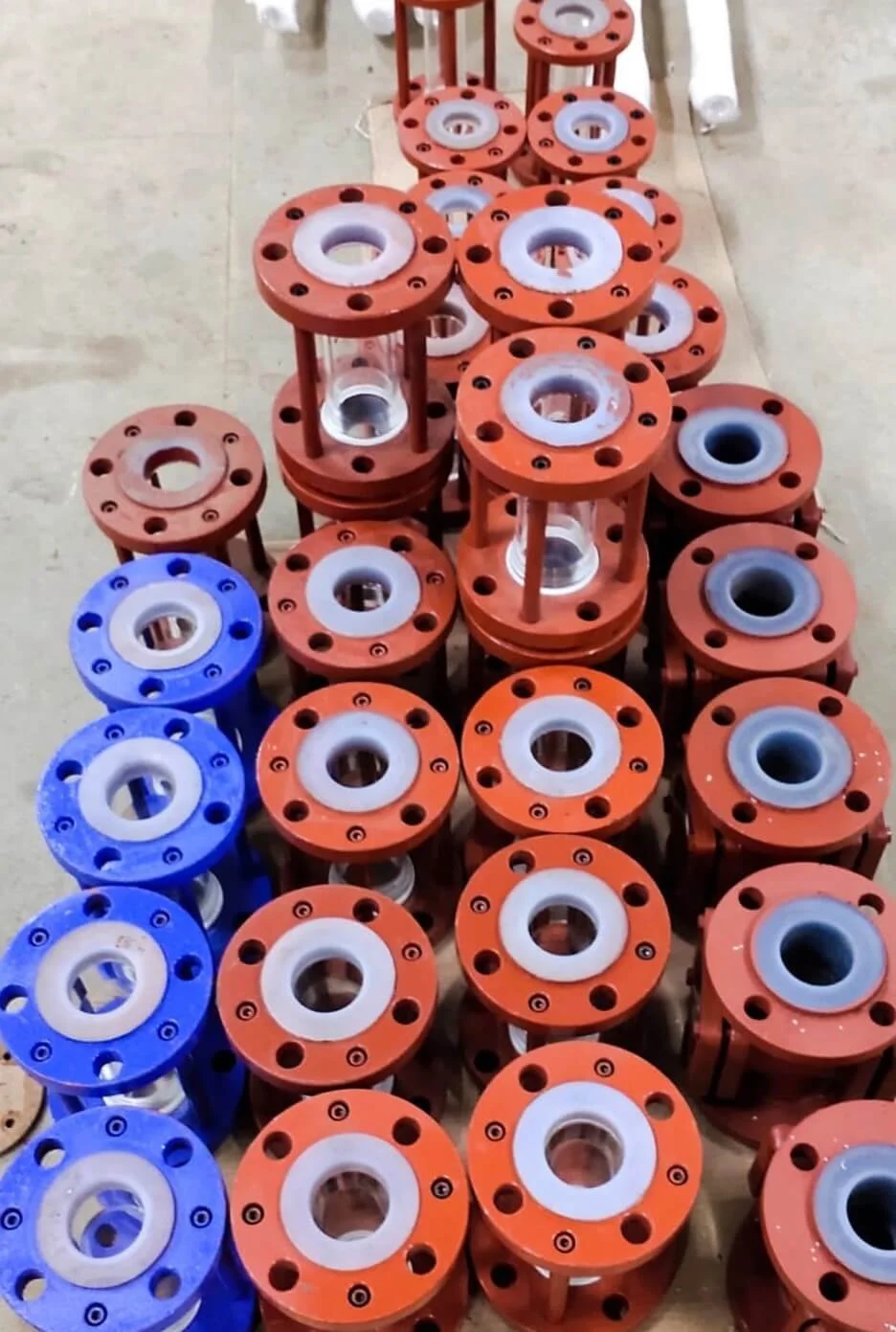
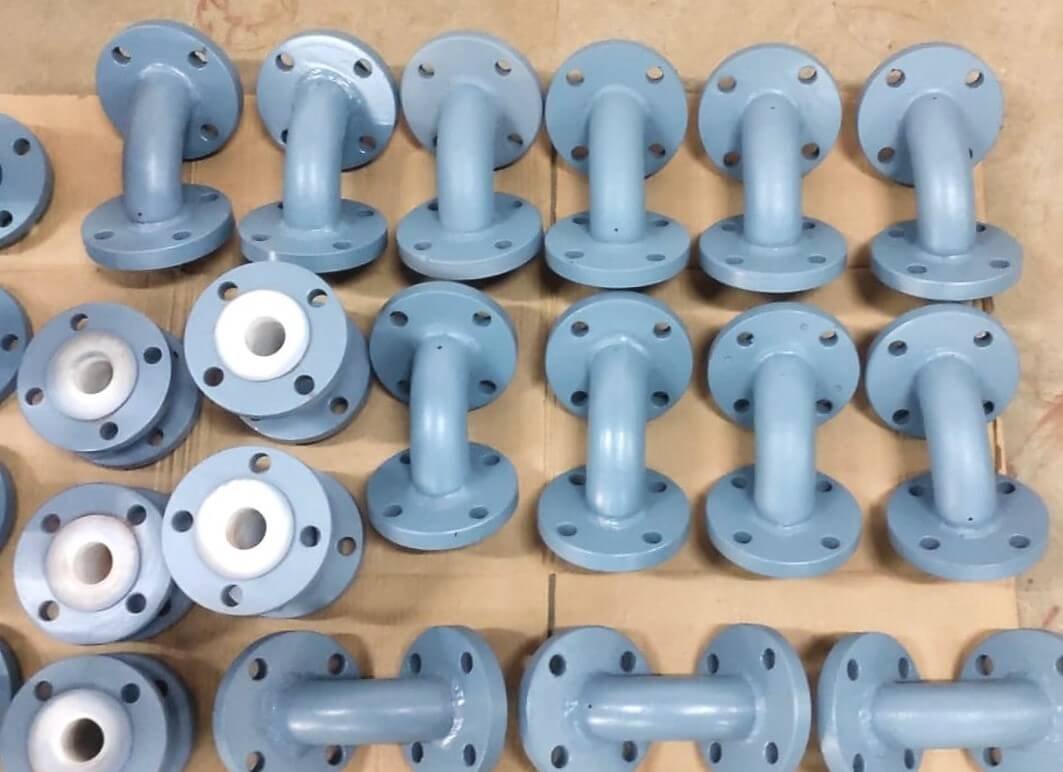
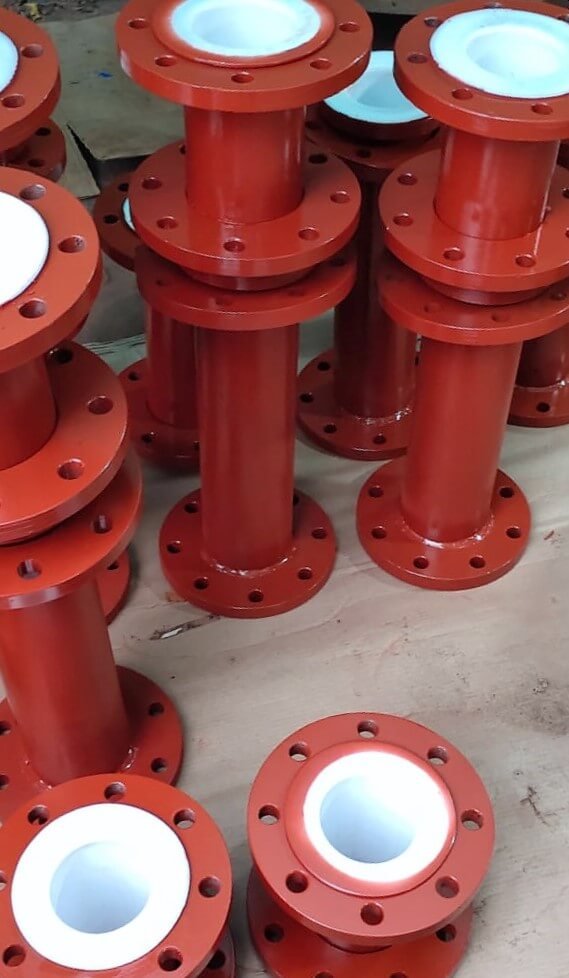
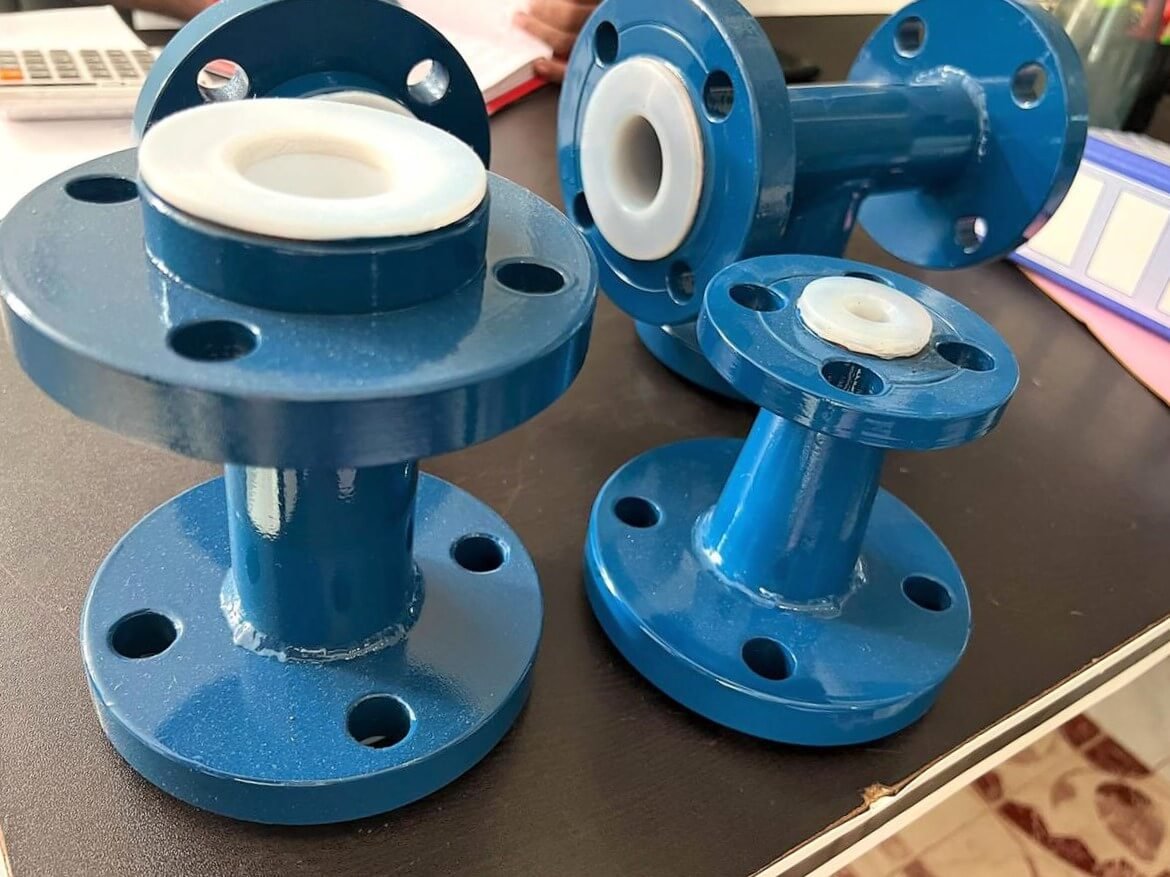
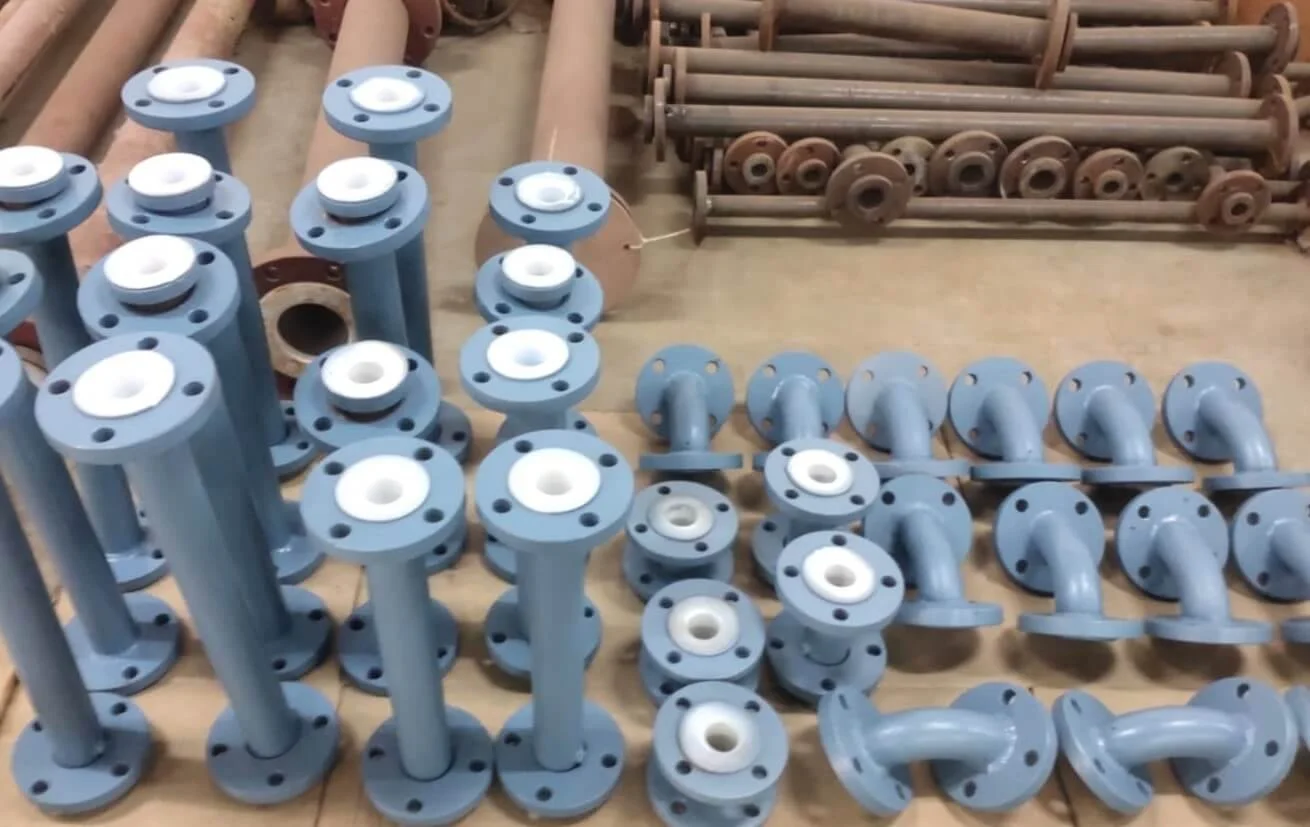
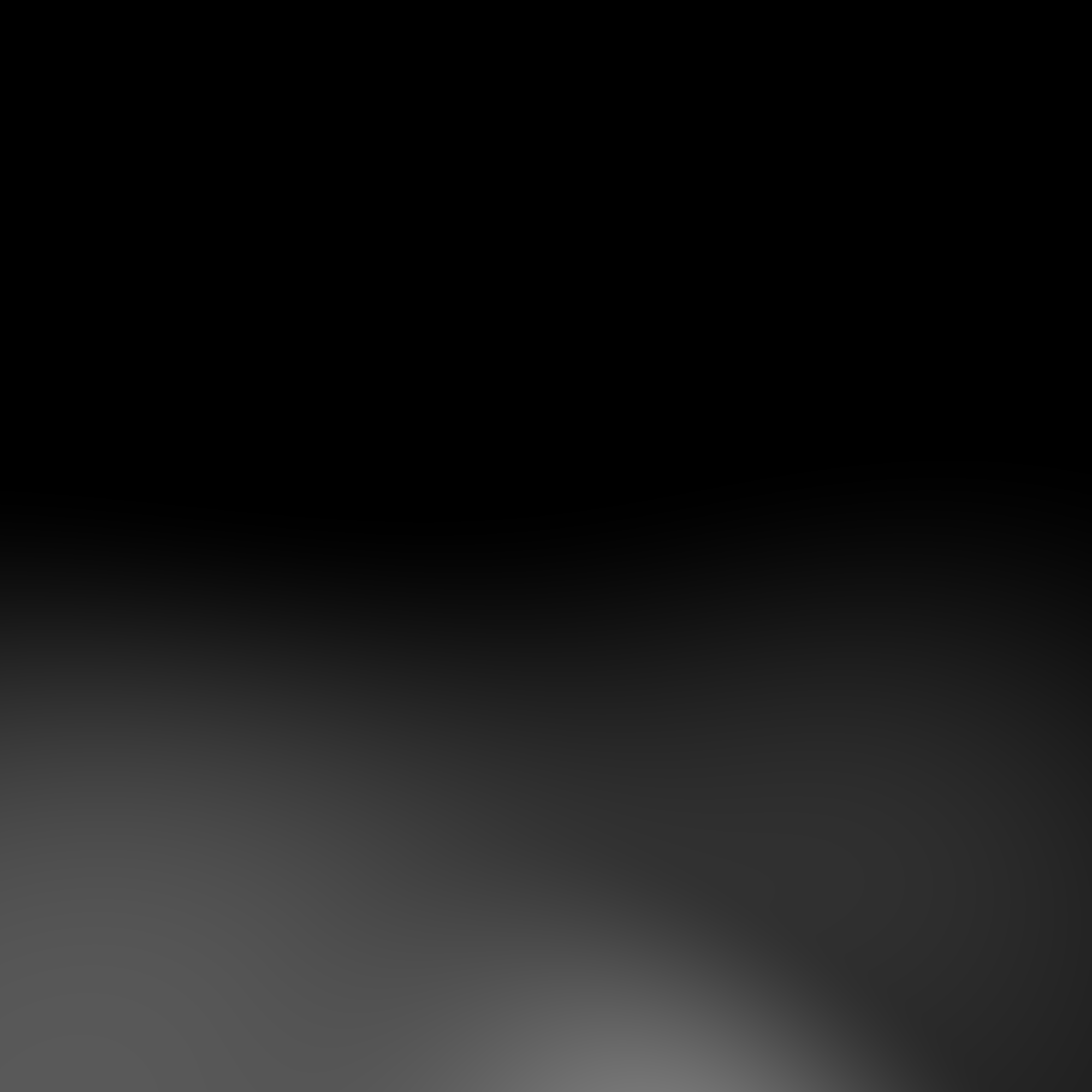
The A1-POLY package can include:
Condensers
Nutsche Filter Reactors
Baffles
Stir Props
Storage Vessels
Ultra-High Purity Tanks & Components
Heat Exchangers
Jacketed Steel Reactors
Pressurized Filters
Condensers
Columns
Etc.
Apical also provides:
Installation of Complete Systems
Training for Complete Systems
Installation Manual
SDS Sheets
SOP for Operation
On-Going Technical Support
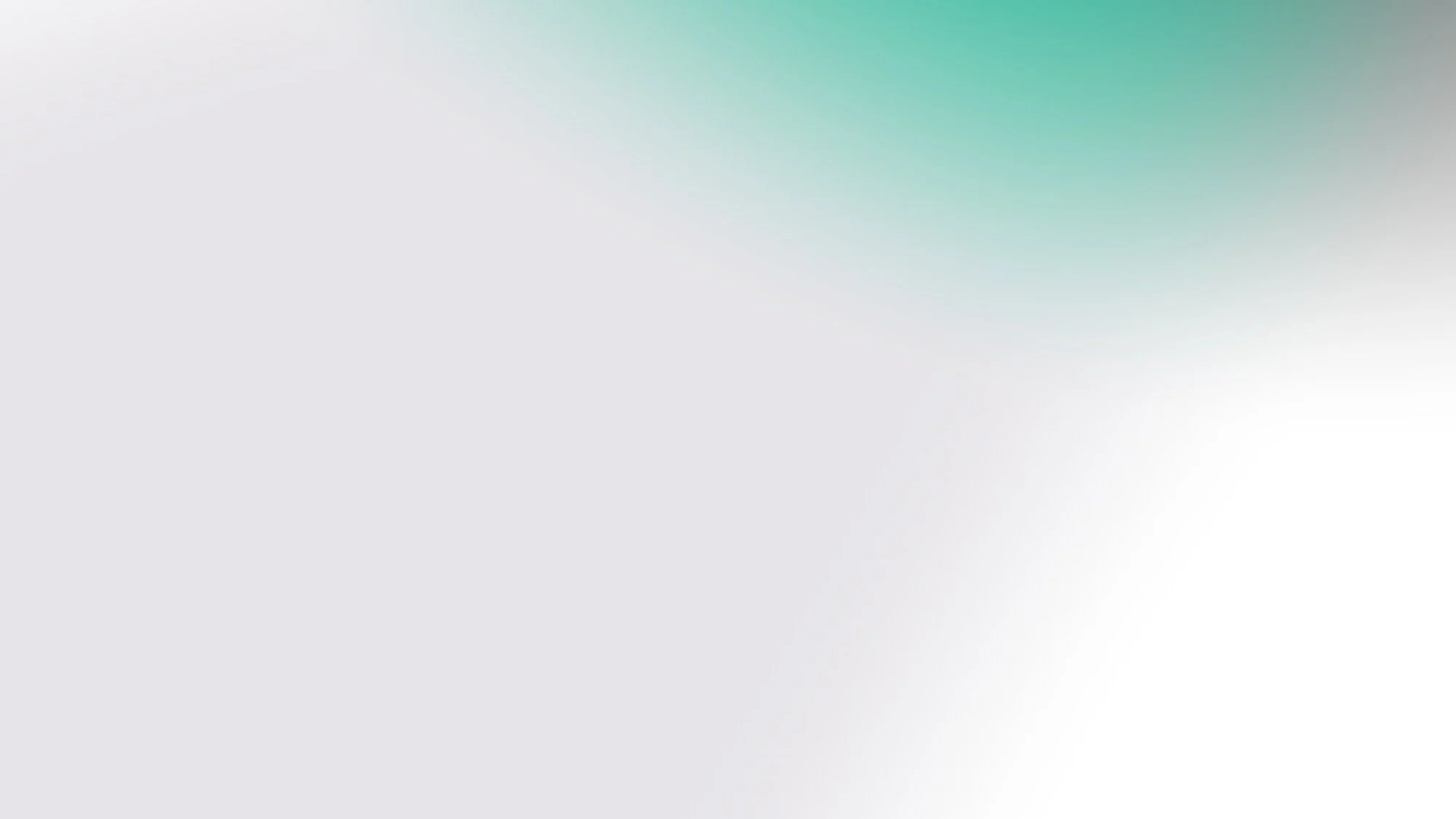
Batch Capacity
63L to 40,000L
Optimized Capacity
80% Total Volume
Typical Start-Up Time
30 Minutes
Typical Batch Runtime
3 to 24 Hours
Temperatures
-60°C to 230°C
A1-POLY series features include:
-
Fitted for deep-vacuum, durability and easy assembly/disassembly, these junctures are fitted with PTFE centering rings & composite clamps.
-
German-made components known for consistency and longevity.
-
Principal vessels are supported by a wide range of attachments and overhead assemblies that require strong, lattice, frame and skid systems to reduce break and increase safety.
-
Reflux of common solvents keeps systems looking and performing brand new for years to come.
-
Small & large vessels and be fitted with lifting systems, allowing for easy cleaning, maintenance and swapping of process vessels.
-
Achieve deep vacuums with temperatures up to 150C and aggressive agitation characteristics.
-
Waste, product & distillates can be continuously ejected from the system while in production.
-
Quickly repaired on-site.
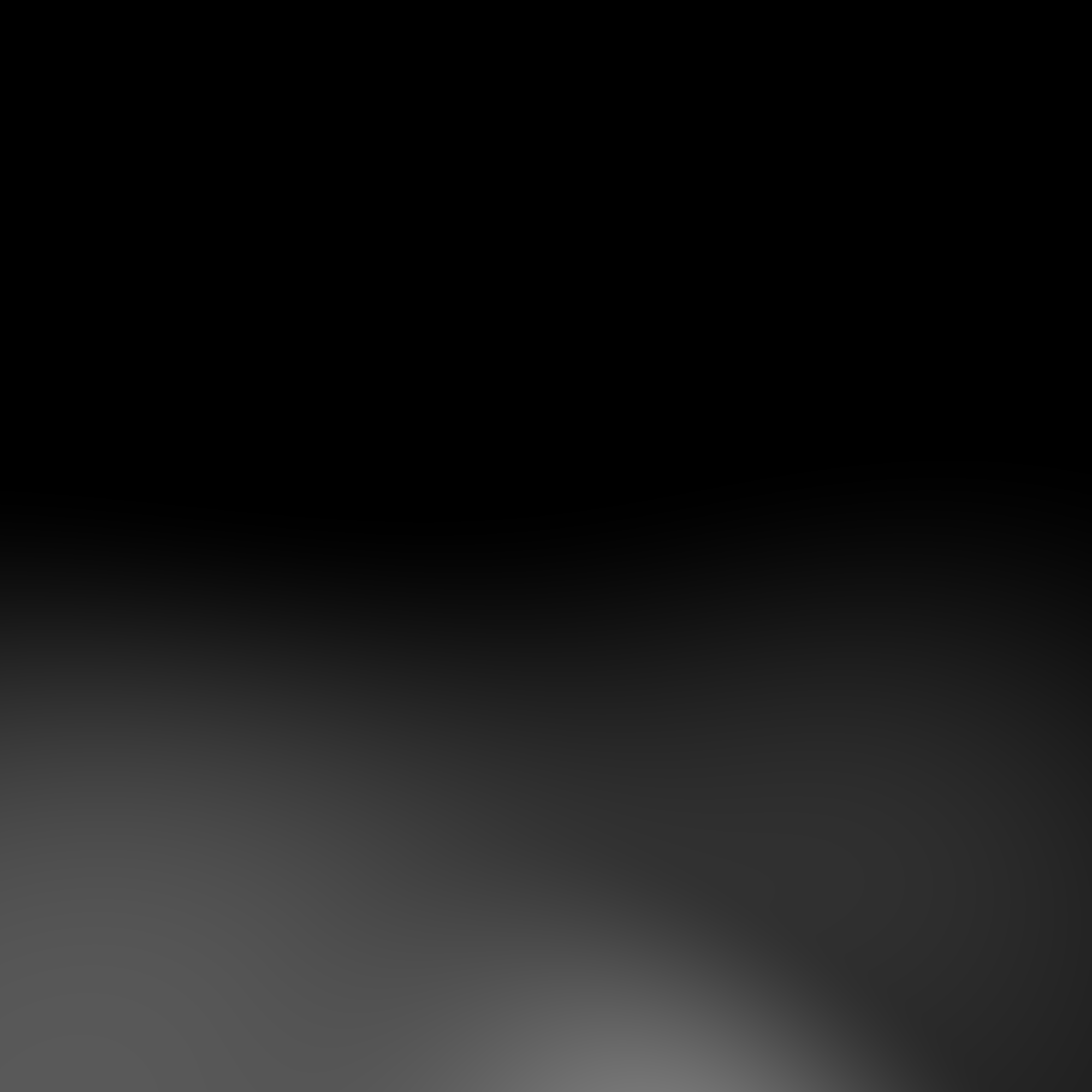