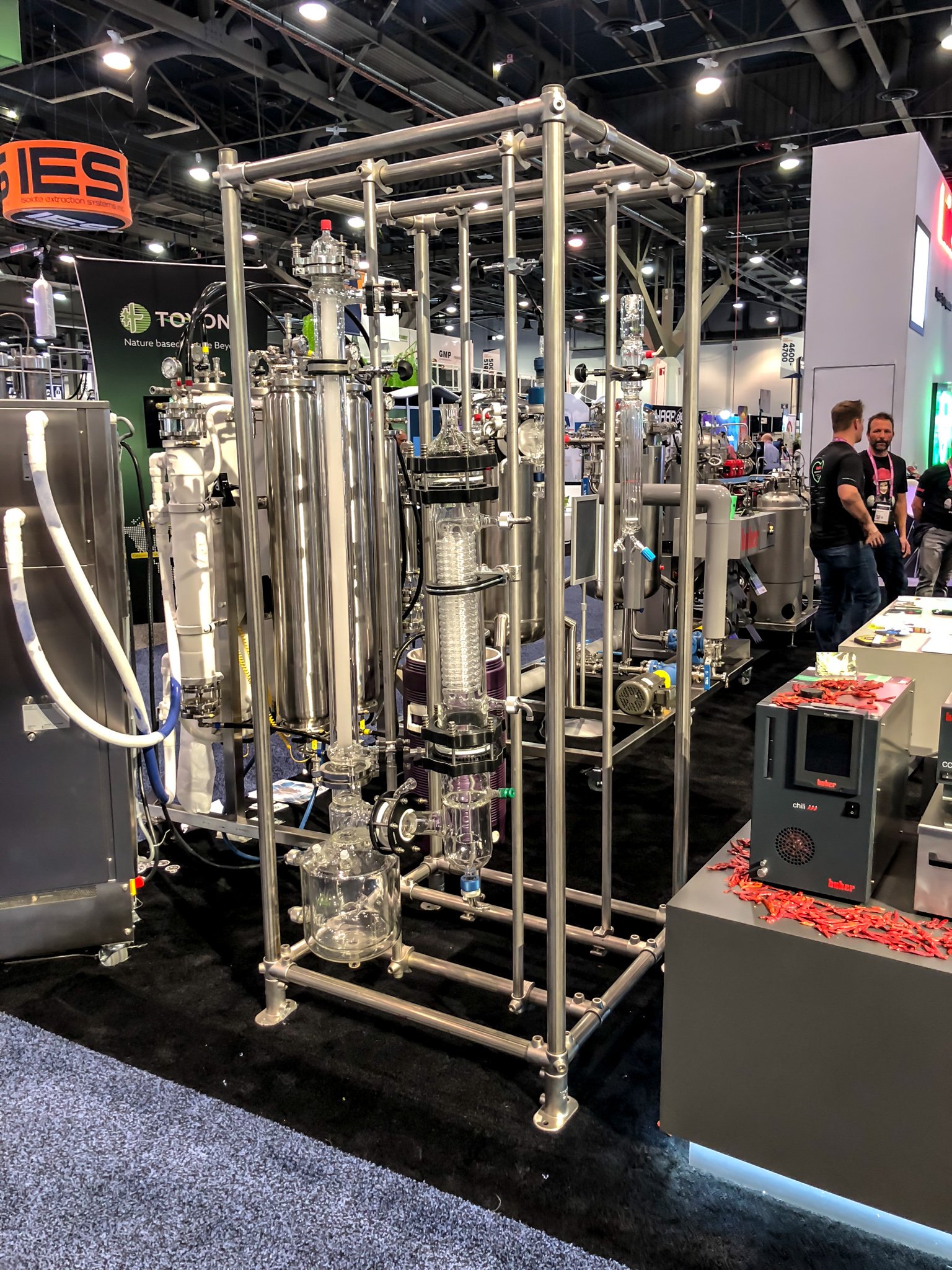
Falling Film Evaporators
A1-FFX Torrential Series
The APICAL A1-FFX Torrential series consists of falling film evaporators (FFE) designed for bulk, continuous and compliant recovery of a wide range of process solvents under vacuum conditions. Operators enjoy the precise control and high throughput while owners rely on the durability, product consistency and protection against contamination Apical systems offer.
Intended to perform low temperature distillations at scale, these systems are a cornerstone of chemical processing across the globe. FFEs most efficiently remove the bulk load of solvent from your product stream and are generally intended to leave 10-20% of solvent in the mixture. A secondary stage is often employed, such as a thin film evaporator, to more efficiently remove the residual solvent left behind.
The A1-FFX Torrential series begins at 10m² evaporative surface area. Systems are scaled to meet the specific project specifications and all ancillary glassware, vessels, motors, temperature control and pumps scale appropriately.
The APICAL A1-FFX Torrential series ranges in sizes beginning at 10m² of evaporative surface area. With solvent recovery throughputs varying significantly based on the at hand, Apical calculates and then sizes FFEs to meet your needs. FFEs are typically employed in scenarios requiring >100LPH of solvent distillation on a pilot-scale, with FFE systems exceeding 10,000LPH regularly within plant-scale processes. Apical has the flexibility to fit systems to your scenario without compromise.
And, with our systems being built to c/EU-GMP and FDA standards, we remain conscious of OSHA safety guidelines. Apical ensures the safety of your operators with the addition of insulation, warning labels, low pressure heat transfer fluids, shielding and comprehensive training.
These systems utilize large tubing to ensure an unimpeded vapor path which is critical to maintaining vacuum at the process rather than just at the pump. With that, systems are insulated for increased efficiency and to meet OSHA specifications for touch burns. Apical engineers these solutions with scale-up being a key factor.
Scaling these dimensions appropriately is one of the keys to high throughputs, successful process development and efficient commercialization.
Apical has taken years of validated field experience and product trials to develop practical technologies that work every day. We combine academic principles with cutting-edge design to provide equipment that can be relied on for years to come with safe, easy operation, high throughputs and consistent product.
No myths about residence time, degradation or physics, no designs with built-in obsolescence, no exaggerations about system capabilities or pay-to-play obstacles to efficient processing.
Apical has tested a wide range of designs under production settings to pierce the veil and remove the mystique around distillations so business operators can focus on the customer and not a daily headache.
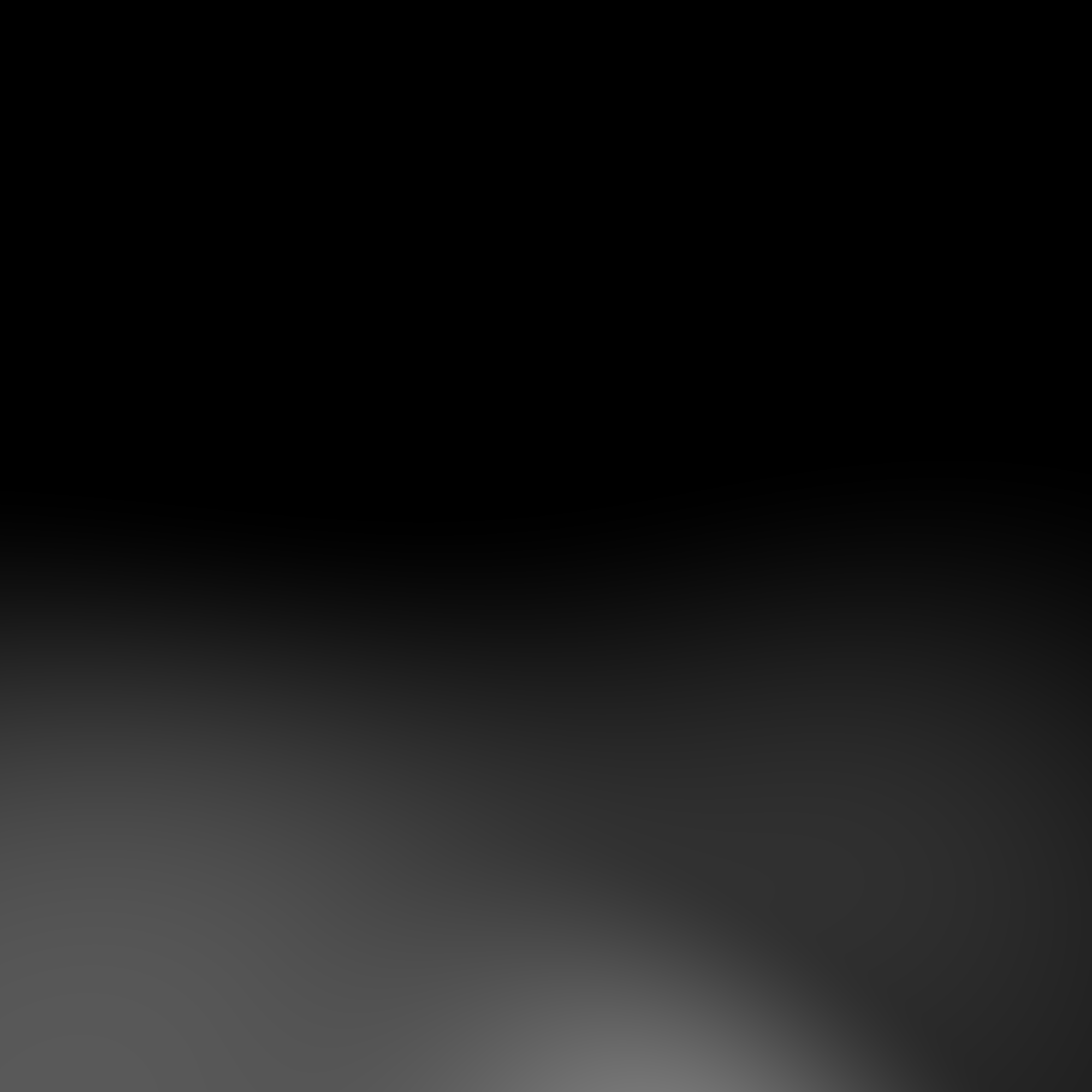
A1-FFX Torrential Series packages include:
Glassware
Centering Rings
Clamping Rings
Skid for Kilo & Pilot
Lab Arms & Supports
Insulated Hoses & Piping
Injection Pump
Concentrate Ejection Pump
Solvent Ejection Pump
Heater for Feed Tank & Lines
Heater for Main Body Jacket
Chiller for External Condenser
Diaphragm Valve
Vacuum Pump
Vacuum Control
Electric Cold Trap
Apical also provides:
Installation of Complete Systems
Training for Complete Systems
Installation Manual
SDS Sheets
SOP for Operation
On-Going Technical Support
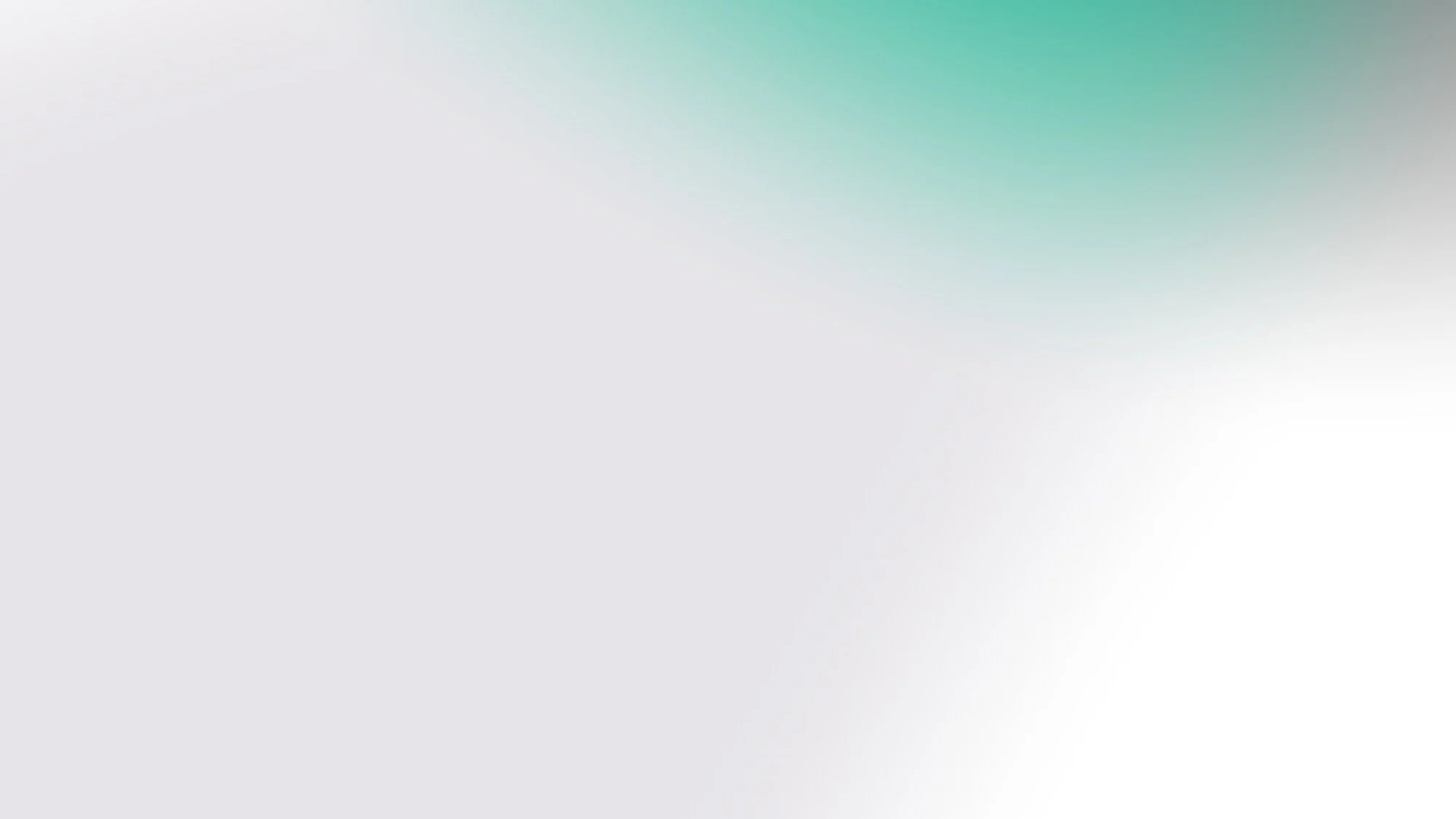
Continuous Systems Built for 24 Hour Operation
Solvent Distillation Rate
>=100LPH (water)
Typical Start-up Time
30 Minutes
Typical Runtime
10 Hours
A1-FFX Torrential Series Features:
-
Ensure leak-free fitment and ultimate vacuum potential for the system.
-
Grooved PTFE wipers ensure a consistently thin film for maximum evaporation and ultimate control of feed retention time.
-
Triple-coil, high surface area system supported by a high-flower chiller.
-
Captures light molecular compounds like terpenes and aromatic residual solvents while protecting the pump and reducing maintenance.
-
Retains heat & energy within the system to maximize efficiency while protecting from touch burns per OSHA standards and allowing the operator to see what is happening.
-
Reduces impedance on vapor path which improves vacuum depth and overall throughput.
-
Tubing where hot liquid can potentially pass or collect is vacuum insulated to prevent touch burns.
-
Fitted for deep-vacuum, durability and easy assembly/disassembly, these junctures are fitted with PTFE centering rings & composite clamps.
-
Principle glassware is meant to be permanently installed on the lattice to limit operator interaction.
-
Reflux of common solvents keeps systems looking and performing brand new for years to come.
-
Loaded solvent is preheated
before being injected into the system to ensure the highest and most consistent distillation rates. -
Concentrated liquors can be ejected to secondary solvent recovery during process while under vacuum.
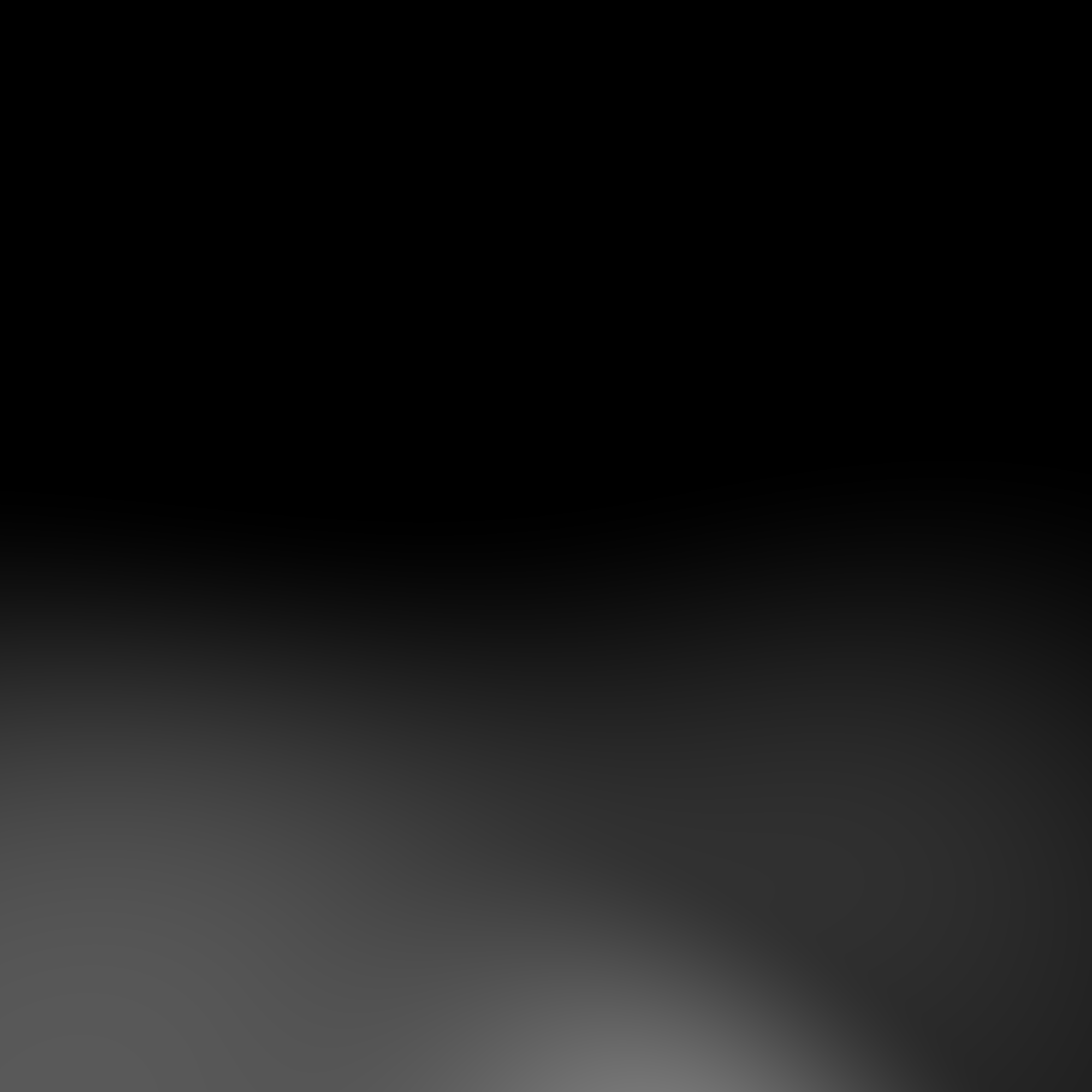