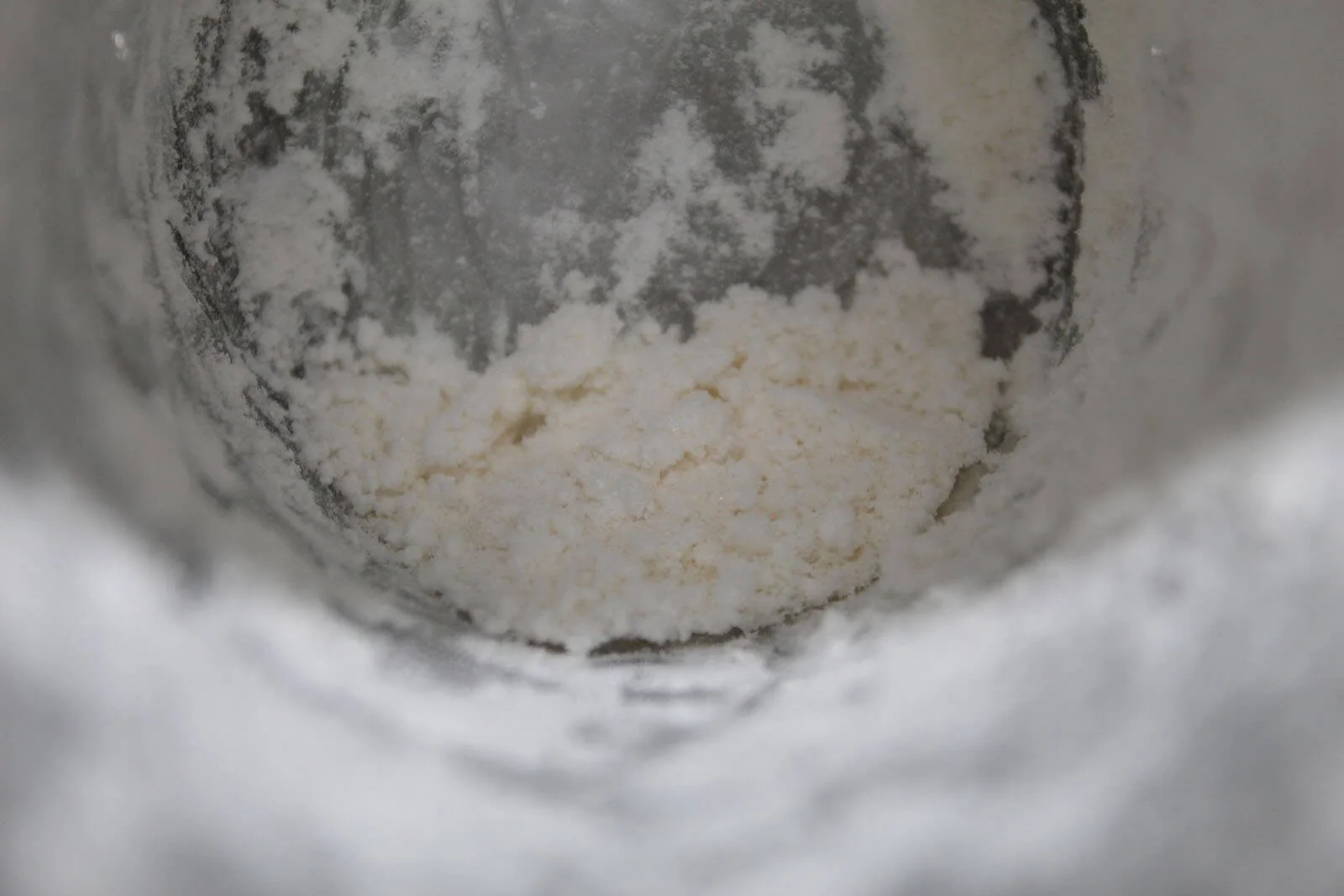
(NUTSCHE) FILTER-DRYERS
Filter-Dryer
Ideal system for precise crystallizations & filtration of fine particles from large volumes. Incorporating the flexibility, control & efficiency of a reactor with the unique power of filtration creates a novel system that plays a critical role in modern chemical processing.
Filter dryers are generally applied to large crystallization processes where a uniform powder or sand is formed in a slurry. Mother liquor is separated from the pure particles and a cake forms on the filter plate surface. The washing & drying of said cake is done in-vessel to reduce operator interaction, product loss & contamination. And, thanks to operation at significant pressures & full vacuum, large amounts of solids can be collected at a very tight micron. With that, the filter dryer is an ideal pairing for the collection of fine particles from larger upstream reactor volumes.
-
50L up to 40,000L
All utilizing DIN standard manufacturing.
-
Mild & stainless steel variants
Exotic alloys like C276, tantalum, etc.
Glass & polymer-lined steel
-
-100 °C to >200 °C
-
<10^-2 torr to >100psi
ASME/CE stamps pressurized vessels & jackets.
Single, double & triple-wall vessels with spiral baffling available.
Optimized wall thicknesses, best suited to both insulate the process from the laboratory and affect transfer of energy from the recirculator to the process.
Ring/spiral-baffling for the heat transfer jacket is optional, but offers faster processing time & better temperature control.
Removable lower filter plates and roll it away.
Easy access to the vessel for deep cleaning when reflux is not enough.
Stationary/permanent installations and castered skids for a wide range of modular systems.
A number of mixing options, agitators & baffles.
Apical filter reactors are built to perform under a wide range of conditions to precise product standards. The system’s versatility has been proven in the field and applied in a surprising variety of processes, often developed as an ideal process-specific solution to simplify the workspace. Whatever the application, Apical will meet both the rigorous requirements of the field and today’s chemists.
APICAL A1-NFD Blizzard Series
Intended to perform batch reactions and isolations in a clean, efficient and uniform manner. It is often useful to perform a fine filtration of the liquor when the process is over. But, the APICAL A1-NFD Blizzard Jacketed Nutsche Filter Dryer series is designed around best practices associated with intermediate & API crystallizations.
Offering precise temperature control and strong agitation, filter reactors are well-suited for the crystallization of consistent, ultra-pure powder & sand. The filter plate effectively retains solids, preventing product loss and increasing the viability of crystallizing small molecules. And, the incorporation of vacuum and pressure significantly increased the flexibility in performing difficult crystallizations as well as drying thick cakes composed of small particles.
These systems are chemical industry workhorses for a wide range of processes that also include isomerization, LLE, bulk fine & media filtration.
Apical has taken years of validated field experience and product trials to develop practical technologies that work every day. We combine academic principles with cutting-edge design to provide equipment that can be relied on for years to come with safe, easy operation, high throughputs and consistent product.
Filter reactions are our bread & butter.
We’ve used them all, run dozens of processes, hundreds of times. We’ve blinded filter plates and made a mess. We understand the tiny details that go into smooth operation.
With that, Apical reactors have scale-up in mind, maintaining consistent ratios of dimension as they grow to ensure a reliable transition to larger processing.
And, when scaling the ancillary systems, Apical works with trusted manufacturing partners known for their robust support staff and resilient equipment.
Considering these finer points is one of the keys to high throughputs, successful process development, facility safety and efficient commercialization.
Systems are built to DIN and cGMP standards for consistent production as well OSHA guidelines for safety. Apical takes industry guidelines seriously to ensure limited downtime, straight-forward audits and predictable operation.
The A1-NFD Blizzard Jacketed Nutsche Filter Dryer series has a wide range of jacketed reactor configurations with our unique design features and efficiency-minded details differentiating our systems in a crowded marketplace.
Our alloy systems range from 50L to 40,000L.
With that, Apical has the flexibility to fit systems to your scenario without compromise.
Apical has tested a wide range of designs under production settings to pierce the veil and remove the mystique around chemical processing so business operators can focus on the customer and not a daily headache.

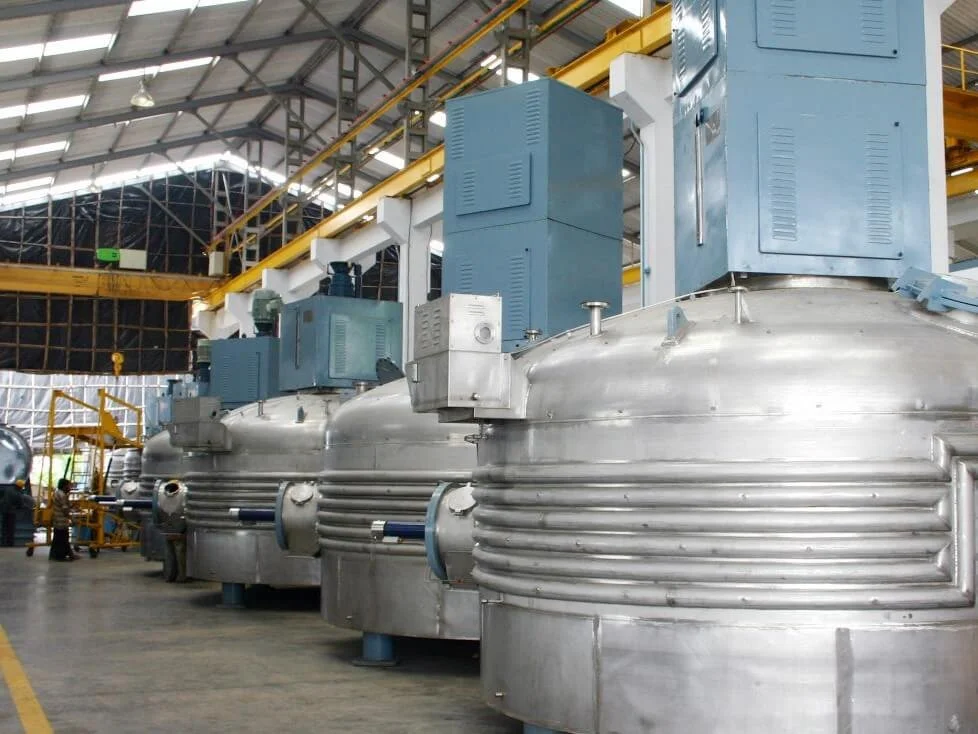
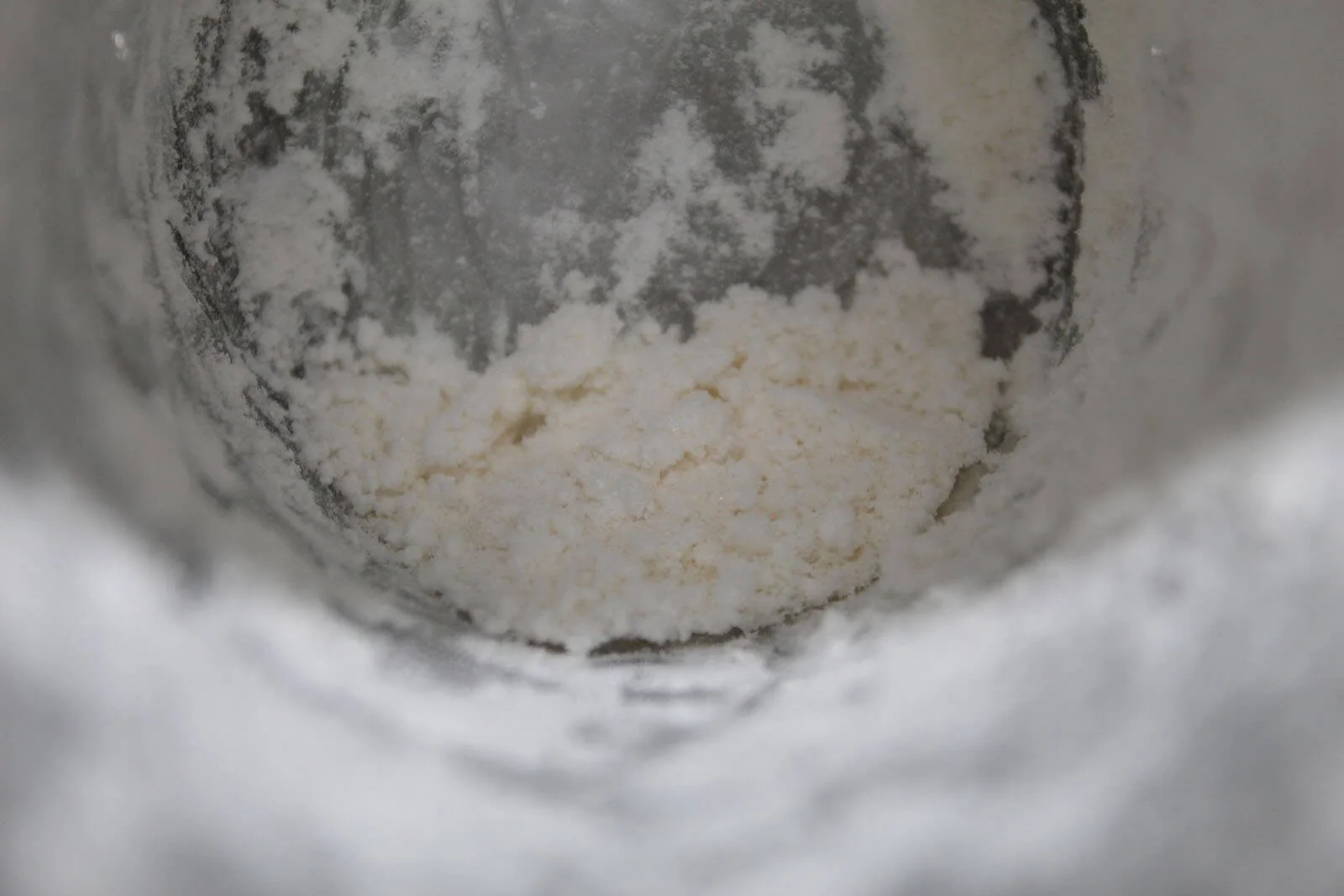


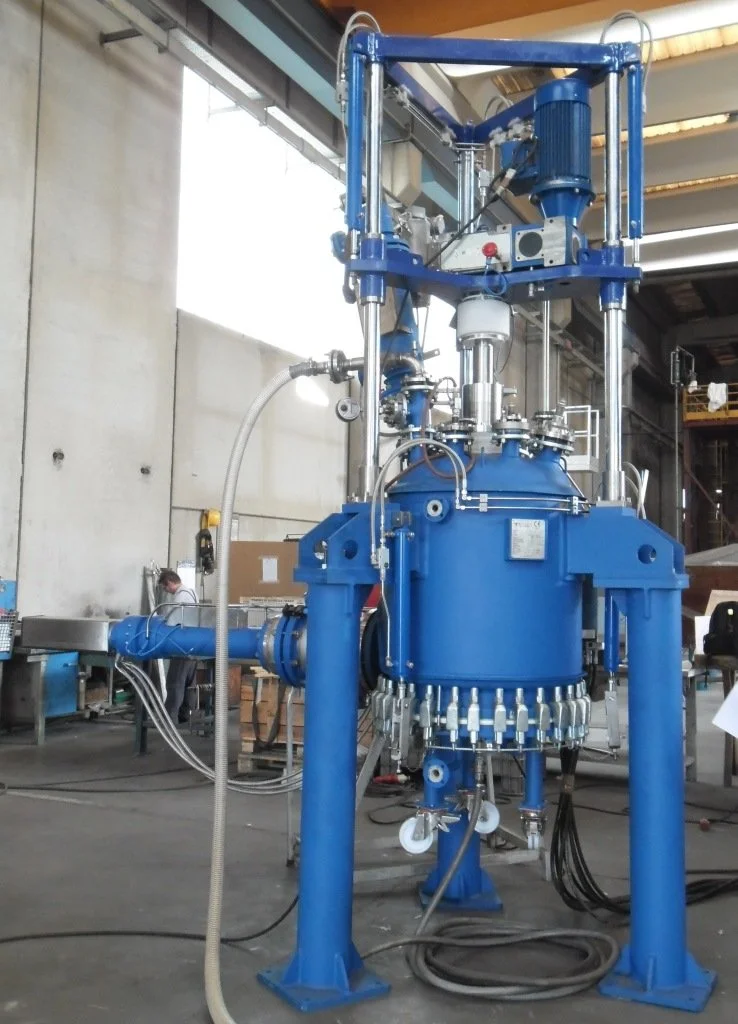
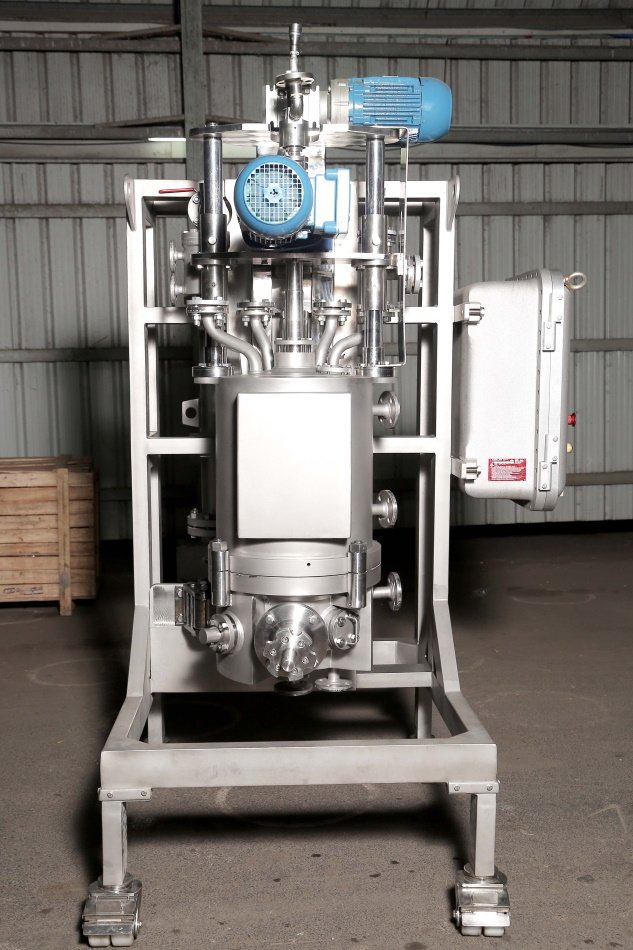
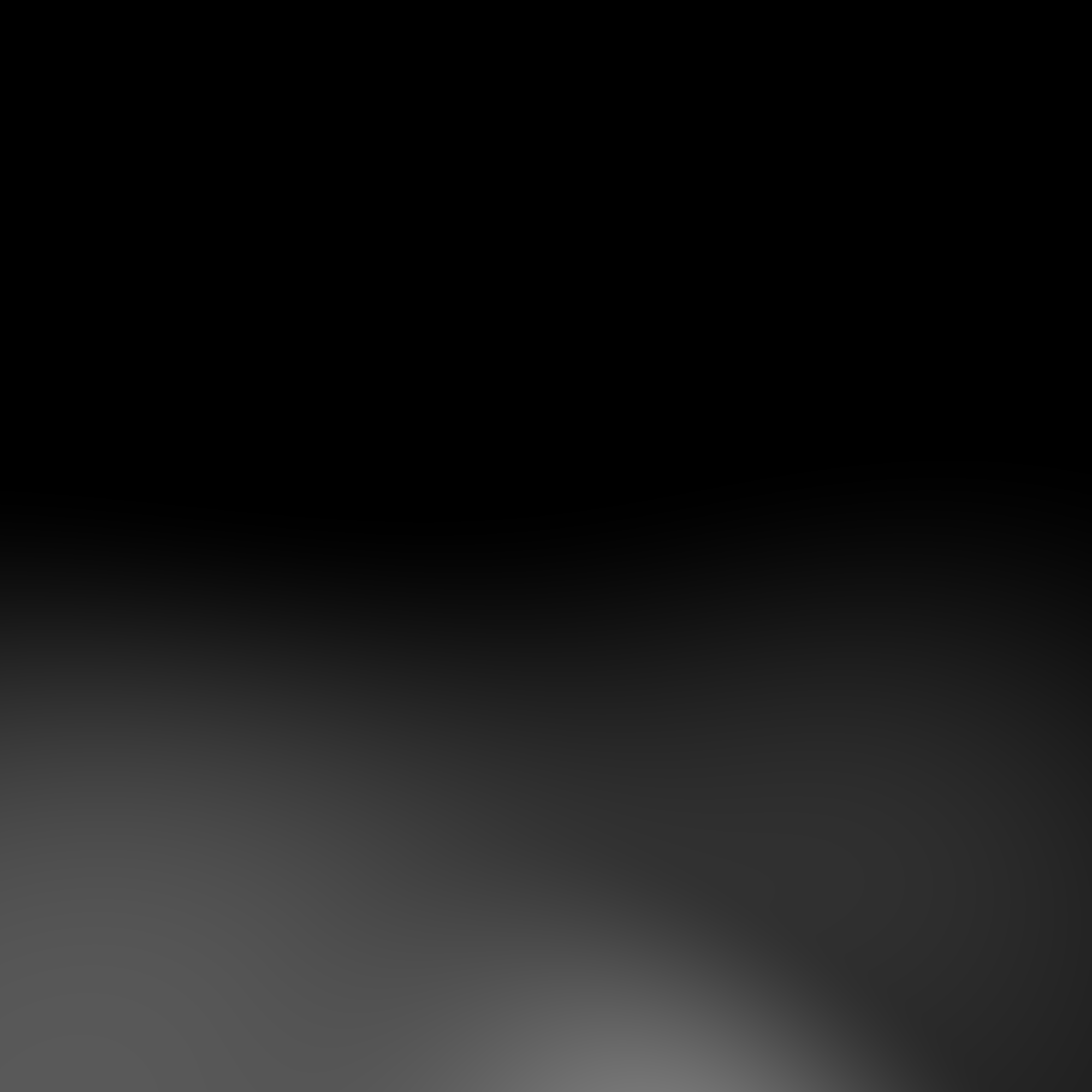
The A1-NFD Blizzard Jacketed Nutsche Filter Dryer package can include:
Chiller for External Condenser
Diaphragm Valve
Vacuum Pump
Vacuum Control
Electric Cold Trap
PTFE Filter Plate & Mesh
Fine Filtration Pads
Closed Solids Addition
Glass-Lined/Alloy Vessel & Lid
Distillation Overhead & Receiving Components
Stir Motor
PTFE-Lined, Hastelloy etc. Stir Prop
Injection & Ejection Gear Pumps
Heater for Feed Tank & Lines
Recirculator for Jacket
Nitrogen Generator
Pressure Relief
Liquid Temperature & Level Monitoring
Centering & Clamping Rings
Lattice Support for Bench-Top
Castered Skid for Kilo & Pilot
Support Structure
Insulated Hoses
Etc.
Apical also provides:
Installation of Complete Systems
Training for Complete Systems
Installation Manual
SDS Sheets
SOP for Operation
On-Going Technical Support
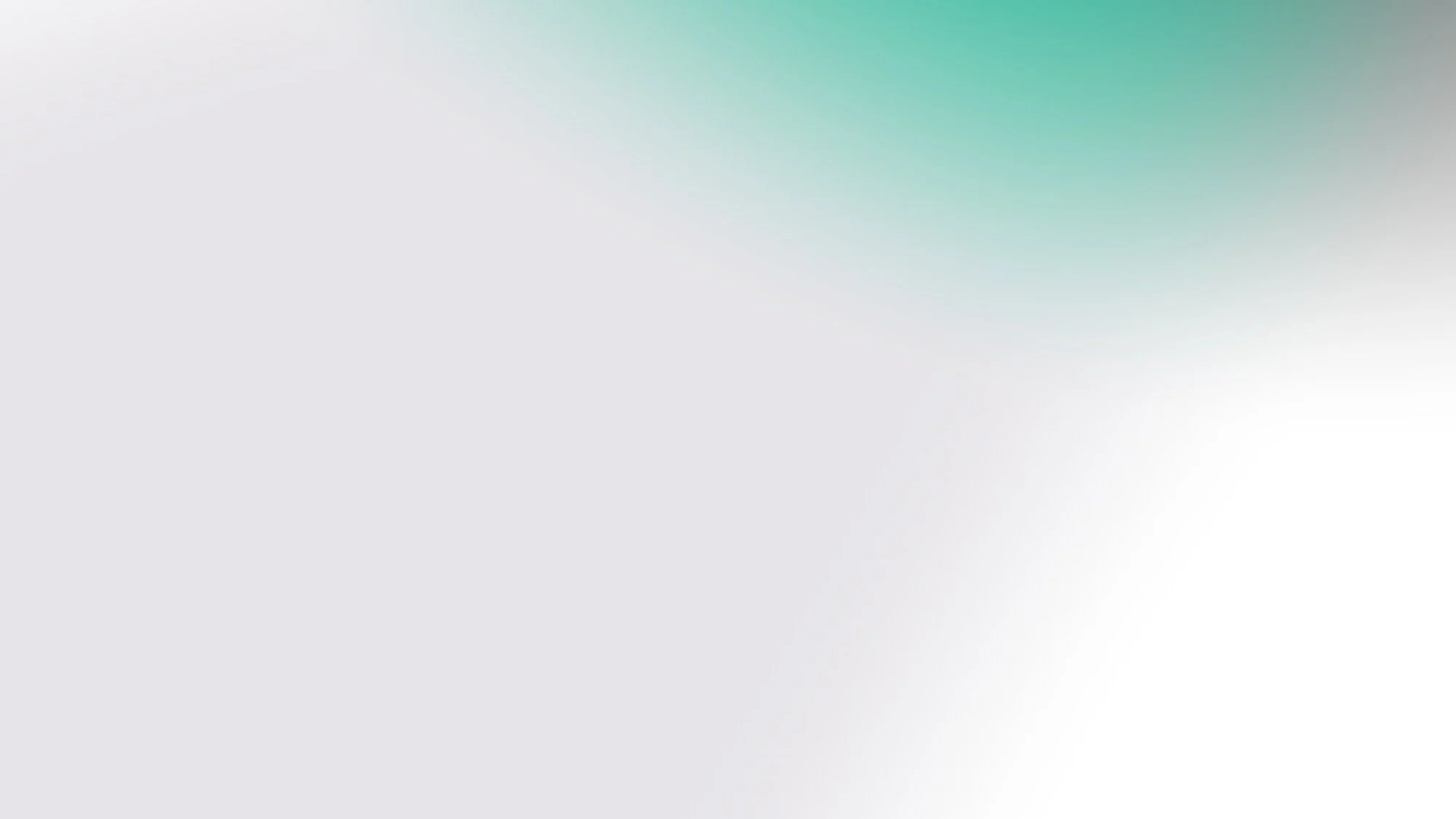
Batch Capacity
50L - 20,000L in Various Linings & Alloys
Optimized Capacity
80% Total Volume
Typical Start-Up Time
30 Minutes
Typical Batch Runtime
2 to 24 Hours
A1-NFD Blizzard Jacketed Nutsche Filter Dryer series features include:
-
Utilize solvent reflux in work-up and cleaning or rely on a PTFE spray to introduce cleaning chemicals.
-
Retains heat & energy within the system to maximize efficiency while protecting from touch burns per OSHA standards and allowing the operator to see what is happening.
-
Filter plates milled for easy flowability but good filter pad support to prevent tears, product loss and leaks.
-
Added turbulence increases efficiency of the recirculator, balances temperature throughout the condenser to improve condenser capacity and is vacuum-insulated to prevent touch burns.
-
Tubing where hot liquid can potentially pass or collect is vacuum insulated to prevent touch burns.
-
Fitted for deep-vacuum, durability and easy assembly/disassembly, these junctures are fitted with PTFE centering rings & composite clamps.
-
German-made components known for consistency and longevity.
-
Principle glassware is meant to be permanently installed on the lattice, frame or skid to reduce breakage and increase safety.
-
Reflux of common solvents keeps systems looking and performing brand new for years to come.
-
Small & large vessels and be fitted with lifting systems, allowing for easy cleaning, maintenance and swapping of process vessels.
-
Mother liquors can be collected in batch carboys that can be separated from the system during production.
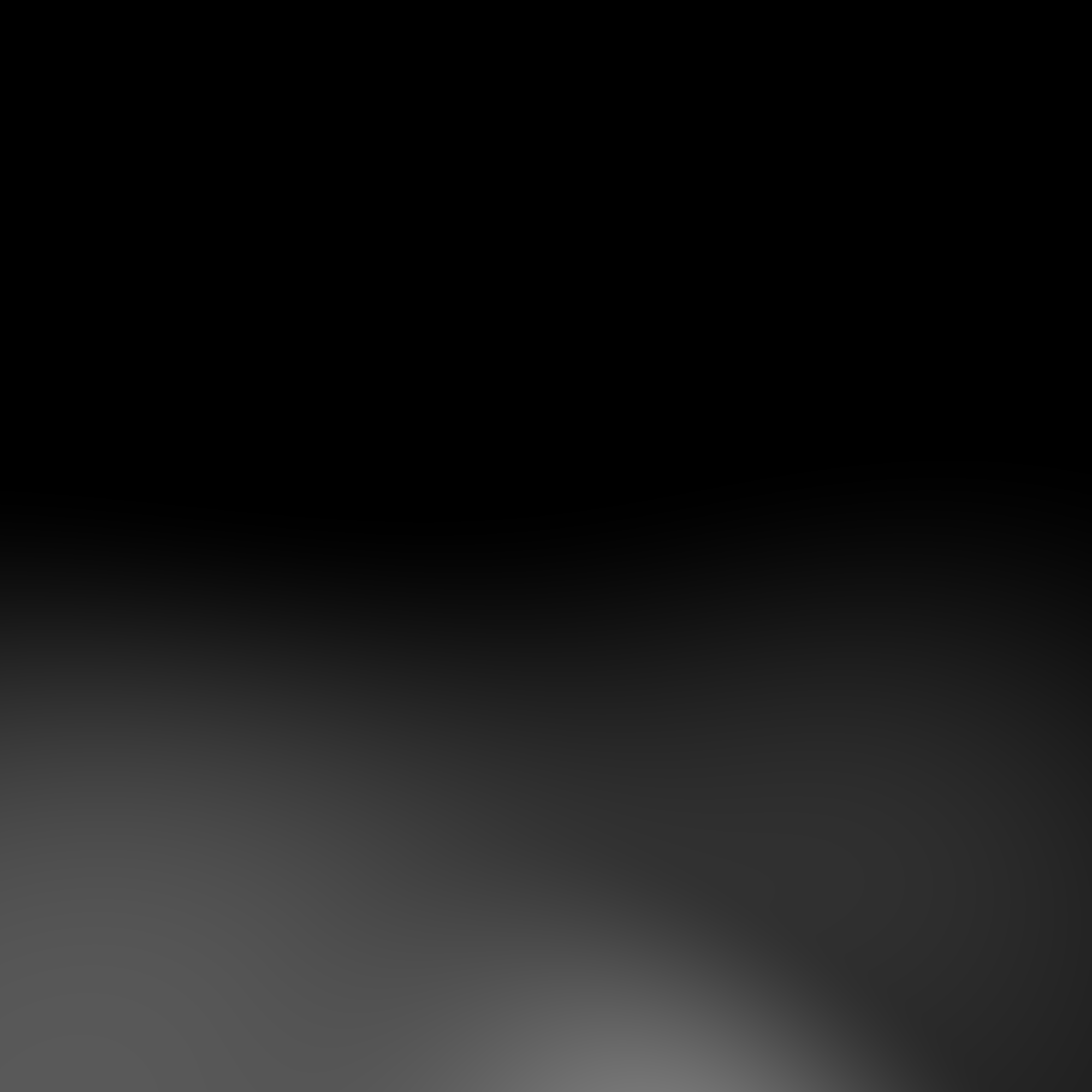